前言
2013-2014年期间,我公司一客户有款乘用汽车后桥被动齿轮,在售后市场出现了5例断齿故障,最短行驶里程为2455KM,最长为44906Km严重影响了客户的品牌形象,同时也削弱了我公司的市场竞争力,给公司的经营带来了负面影响。
断齿是齿轮最严重的失效形式,失效后,齿轮的传动功能丧失,后桥不能实现力矩的传动,车辆不能正常行驶,容易发生事故造成人身伤害,为此对该后桥齿轮打齿问题进行立项运用《质量工具》分析。
一、项目选择
1、失效齿轮信息
打齿齿轮售后信息
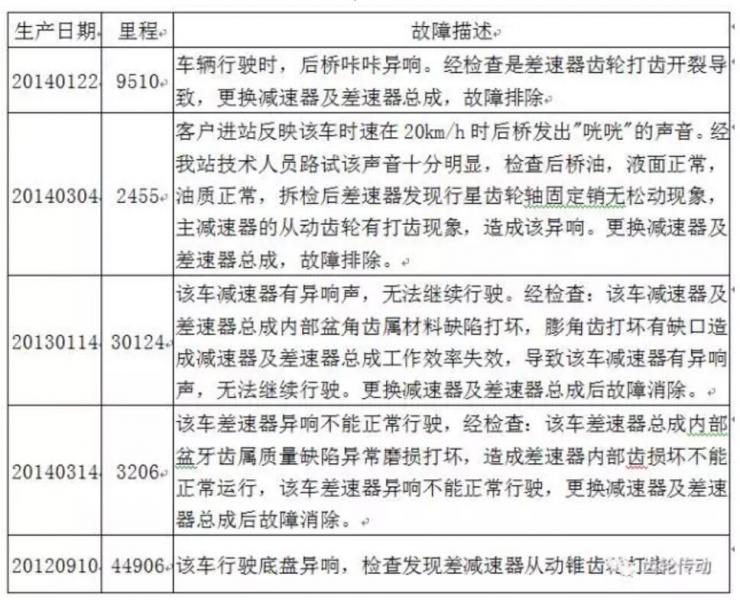
2、对失效齿轮断口进行描述
失效件一断裂特征:
断裂齿数:3齿
断裂部位:中间偏大端位置,齿顶断裂,裂至齿根处约4-5mm
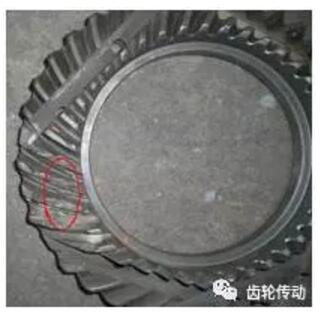
失效件二断裂特征:
断裂齿数:4齿
断裂部位:中间和大端位置,齿顶断裂,裂至齿根处约4mm左右
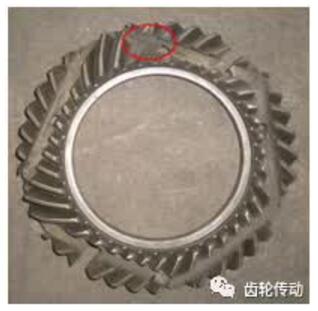
失效件三断裂特征:
断裂齿数:3齿
断裂部位:中间位置,齿顶断裂,裂至齿根处约1mm左右
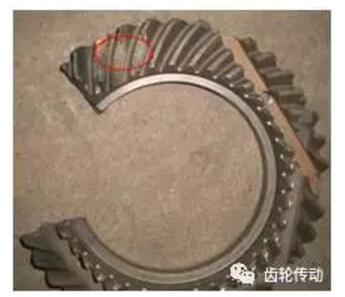
失效件四断裂特征:
断裂齿数:3齿
断裂部位:中间偏大端,距小端约5mm左右的位置,其中有1齿在大端齿根圆角处断裂。断至齿根
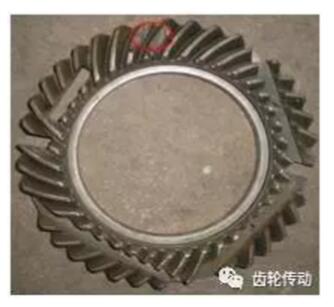
失效件五断裂特征:
断裂齿数:3齿
断裂部位:其中1齿中间偏大端的齿根圆角处,另1齿在距小端约4mm左右的位置。
3、对断口形貌分析 4、对裂纹源形貌进行分析
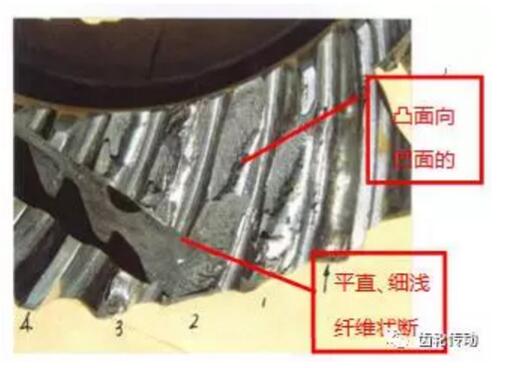
断裂特征:
(1)渗层断裂较平直,深灰色
(2)呈细浅纤维状,从凸面向凹面有一条螺旋角的撕裂岭
(3)断口为弯曲低周疲劳断口
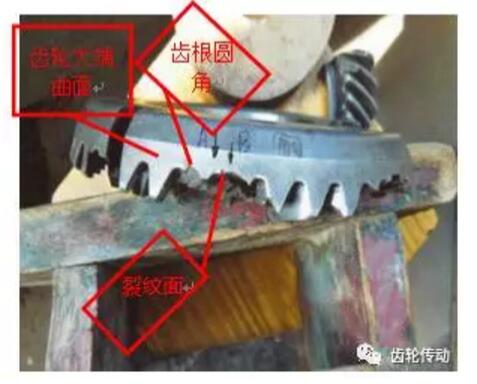
裂纹源特征:
(1)位置:位于齿轮齿根圆角处。(2)形状:裂纹面在齿的大端曲面与齿根圆面向下成约18-20度的角度,断裂位置正是轮齿受力最大的位置。
断口结论:
该5起断齿故障被动齿轮,断裂齿数均3-4个齿,且位于接触区的位置,从齿轮小端走向大端与且是与面锥相交的齿顶处(距离小端约5mm处的中间偏大端)断裂。
5、对断口微观进行分析
断口高倍组织形貌齿面部位金相组织
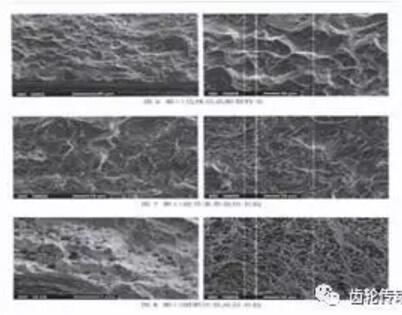
微观主要为沿解理面的穿晶断裂,断口上呈现光泽的小面或沿晶界的晶间开裂(脆性断裂)
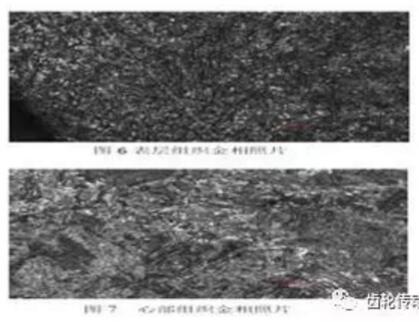
表面组织为针状马氏体、残奥,级别MA
/:3级;碳化物级别K:2级;心部组织为板条状马氏体。
结果:该齿轮的断裂是由于过应力造成的,属弯曲低周疲劳断裂(脆性断裂)。
二、确定产品特性Y
1、齿轮断齿失效机里分析
工作原理:
车辆行驶时,发动机通过传动轴直接将动力(风骏皮卡车型要230N.m)传递到主动齿轮,主动齿轮与被动齿轮啮合,通过被齿两端的半轴将力传递到车轮上。
失效机理:
如果齿轮在运行过程中齿根受到的应力ϬF超过材料本身承受的极限应力ϬFim,即ϬFimYNT﹤ ϬFYθ时,轮齿会出现打齿、断裂故障。
注: YNT为被动齿轮的寿命系数(该系数是根据齿轮的设计寿命要求选取的),当齿轮设计寿命为循环次数≥6ⅹ106时,取 YNT=1。(Yθ为齿轮工作时的温度系数,正常工作条件下取Yθ=1)
综上所述齿轮的材料极限应力Ϭfim和齿根应力ϬF主要决定齿轮打齿的失效程度。
2、运用故障树来分析影响齿轮强度的因素(由于材料的极限应力是根据材料查阅齿轮设计手册来确定的,对于经过渗碳、淬火的齿轮钢材的强度(齿根极限应力为Ϭfim=207MPa)
影响齿轮强度的因素:
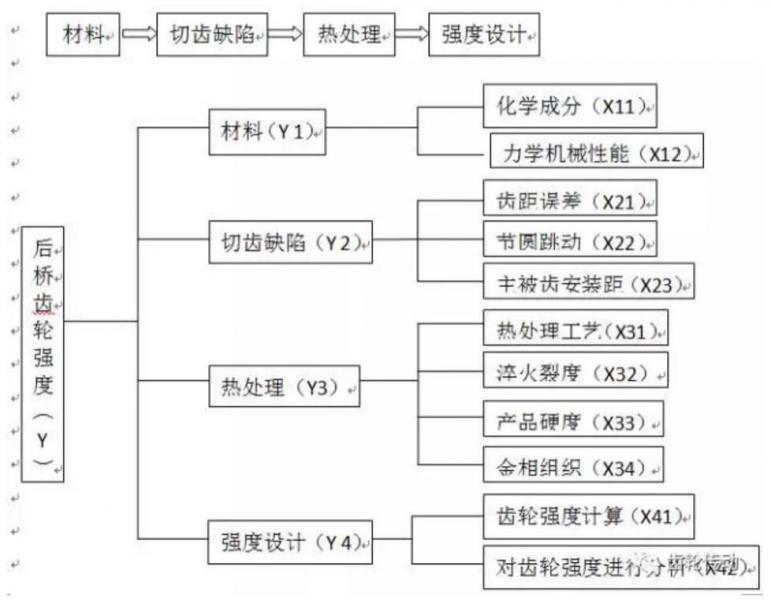
1、对失效件的材料进行分析
(1)化学成分
故障件化学成分检测分析
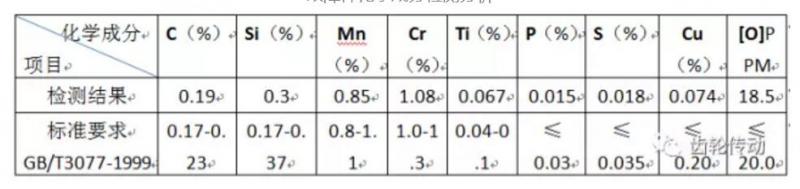
结论:
通过对故障件的材料数据及标准要求对比分析,故障件材料化学成分满足《GB/T3077-1999》中20CrMnTi的元素要求,因此材料的化学成分合格。
钢材进厂的过程控制方法:每批钢材到货后,按钢材不同的规格随机抽取一炉号委托到郑州机械研究所进行化学成分检测。
(2)材料的机械性能
该批钢材机械性能分析
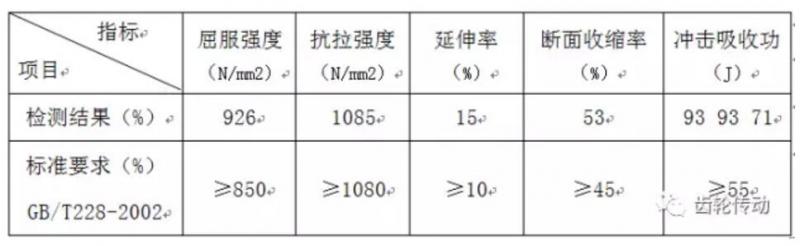
分析结果:
故障件批次材料的机械性能(抗拉强度、屈服强度、伸长率、断面收缩率、冲击吸收功)均满足GB/T228-2002要求。因此材料的机械性能也合格。
过程控制方法:每批钢材到货后,按钢材不同的规格随机抽取一炉号委托到郑州机械研究所进行材料机械性能的检测。
2、对失效件的切齿缺陷进行分析
(1)切齿工艺流程
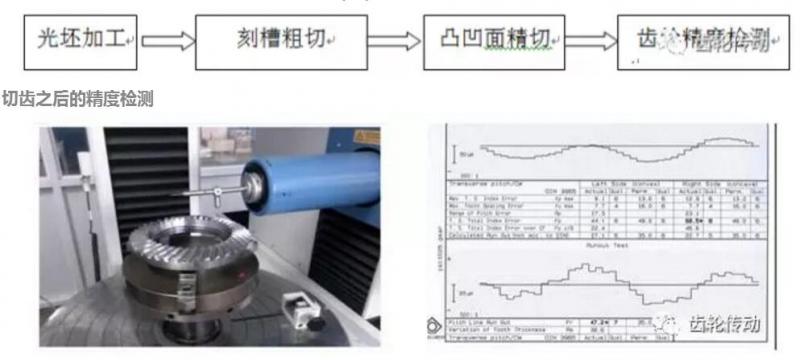
切齿之后的精度检测
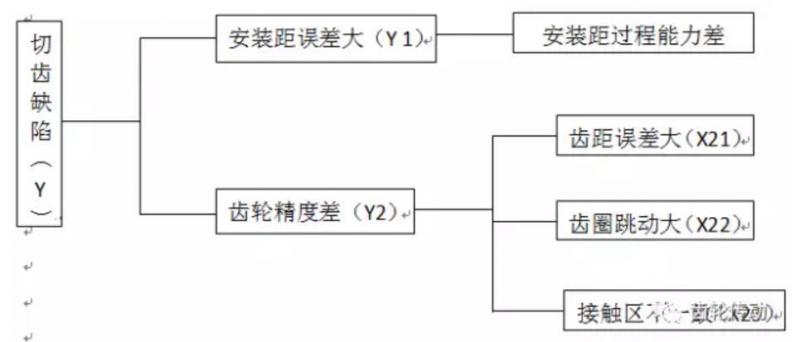
由以上检测报告可以看出,该失效齿轮的精度为8级,齿距误差、累积误差均在6级以内,齿圈跳动为≤0.05mm。由此可见,齿轮切齿加工工序没有什么问题。
对于汽车后桥弧齿锥齿轮(准双曲面弧齿锥齿轮)的加工工艺,一般采用的是光坯在格里森切齿机上进行凸面和凹面一次成型的工艺,热处理后齿部还需要进行配对研磨加工。切齿时易产生的缺陷是齿距误差过大或周节误差过大,安装距不稳定,这样将造成齿轮的接触区不稳定。
(2)对切齿缺陷进行分析
为研究切齿方面的变差,运用树图将产品生产过程中可能存在的切齿缺陷进行了分析。
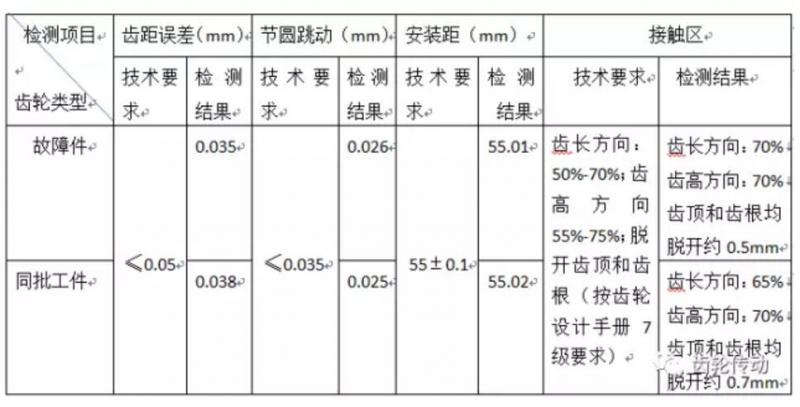
同批次齿轮的质量进行检测
经过对故障件和同批次工件的齿距误差检测,其检测结果如下表:
故障件和同批次工件的齿距误差检测结果(均值)
为了保证本批被齿安装的一致性,用SPC《质量工具》来分析安装距的过程能力:
被齿安装尺寸分析
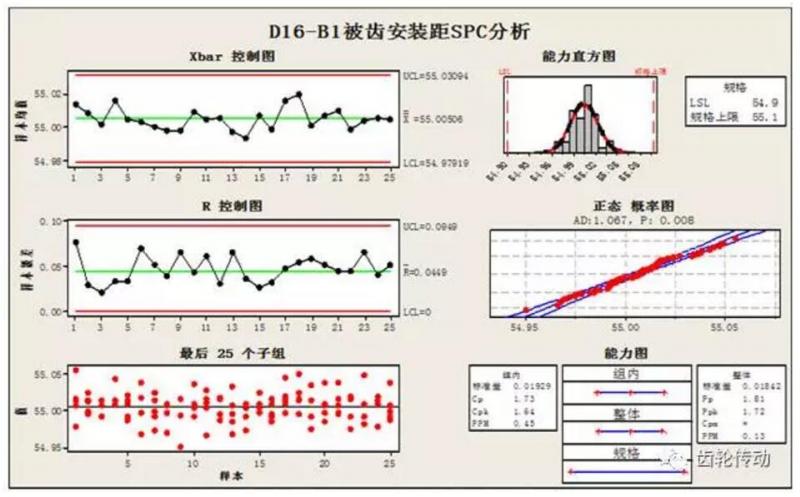
由以上六合图的数据分析可以看出:该被齿的安装距尺寸的过程能力CPK=1.64>1.33,且呈正态分布,说明该切齿过程能力受控,可以批量生产。
3、对热处理缺陷进行分析
(1)热处理工艺简介
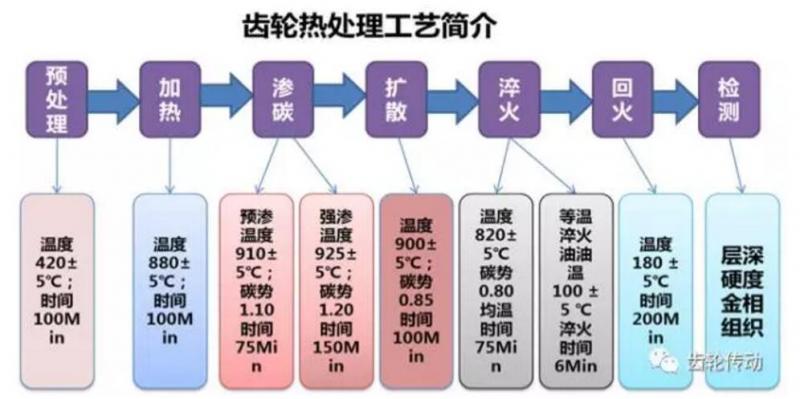
齿轮经过渗碳、淬火、低温回火处理之后,表面得到较高的耐磨性和高的疲劳强度,增加齿轮的抗冲击性能;心部得到较高的强度和韧性,这样齿轮在使用过程中能承受较大的冲击载荷。低温回火能有效地消除或降低淬火过程中产生的内应力、组织应力和脆性,以免齿轮在使用过程中造成轮齿断而失效。
齿轮在热处理时易产生的缺陷渗碳层、表面硬度、心部硬度及金相组织不均匀或者达不到工艺技术要求,如果工艺调整或执行不当,此时还有可能能产生淬火裂纹。
(2)为研究热处理方面的变差,对失效产品进行解剖作硬度、金相等热处理指标的分析:
硬度及金相检测结果
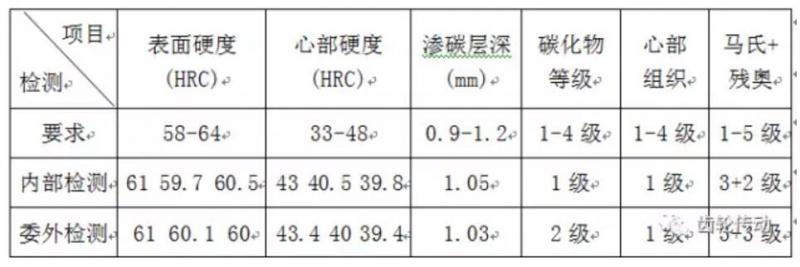
由以上检测结果表明:各项检测结果均在技术要求范围内,说明该齿轮的热处理质量没有问题。
(3)为验证热处理工艺可靠性,运用《质量工具》MSA对产品金相检测记录和该产品金相检测记录进行分析。
a.硬度计MSA
维氏硬度计表面硬度样本数据
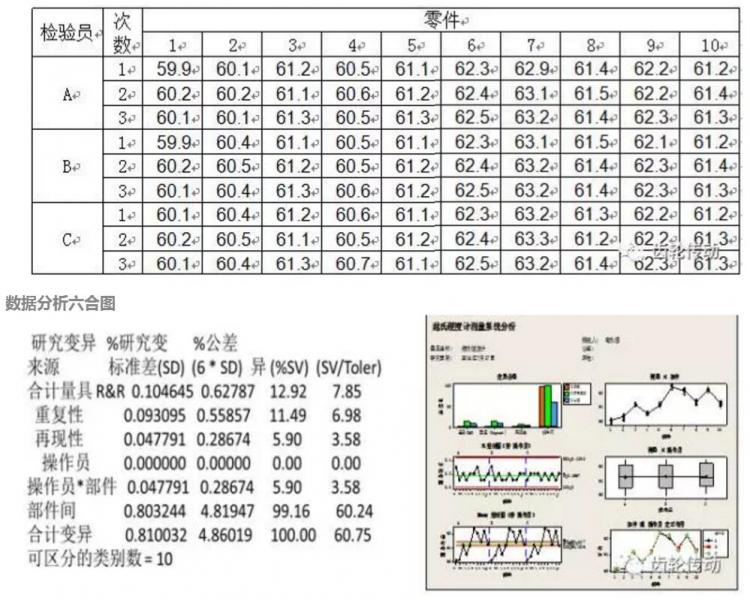
数据分析六合图
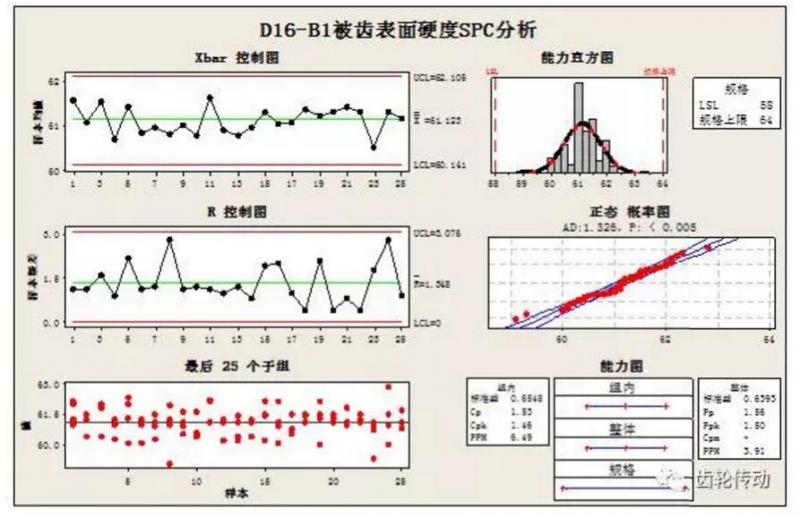
由以上数据可以看出:该测量系统可区分的类别数=10,说明该测量系统的分辨率ndc=10>5。说明该测量系统分辨能力充分满足要求。
b、热处理过程能力(表面硬度)

通过对该故障件表面硬度数据进行分析,该生产系统过程能力CPK=1.46>1.33,说明生产过程受控。
4、对齿轮强度进行计算校核
4.1对齿轮的接触区进行CAE有限元分析
主齿被齿
通过用CAE软件对后桥主被动齿轮接触区作有限元分析得知:当在倒车工况下(齿轮承受扭矩最大时),主齿最大应力发生在齿根中部偏大端处,被齿最大应力发生在齿顶中部偏大端处,同样也反映出齿轮的强度不足,存在有断齿的隐患。
4.2断齿机理分析
工作原理:
车辆行驶时,发动机通过传动轴直接将动力传递到主动齿轮,主动齿轮与被动齿轮啮合,通过被齿两端的半轴将力传递到车轮上。
失效机理:
如果齿轮在工作时齿根受到的应力ϬF超过材料本身承受的极限应力ϬFim,即ϬFimYNT﹤ϬFYθ时,轮齿会出现断裂故障。
注: YNT为被动齿轮的寿命系数(该系数是根据齿轮的设计寿命要求选取的),当齿轮设计寿命为循环次数≥6ⅹ106时,取 YNT=1。Yθ为齿轮工作时的温度系数,正常工作条件下取Yθ=1。
结论:齿轮的材料极限应力Ϭfim、齿根应力ϬF决定齿轮打齿的失效程度。
4.3对齿轮的齿根应力进行计算
《齿轮手册》中,被动齿轮齿根应力(Mpa)计算公式
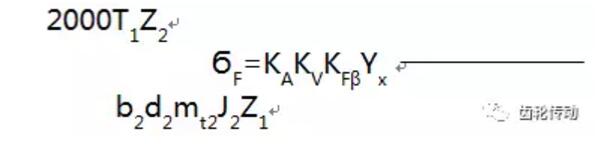
式中系数:
KA为计算强度的使用系数(根据齿轮的使用工况来选择):选KA=1.25。
KV 为动载系数(根据齿轮精度来选择): IQ ≤7 级,KV选1.025
KFβ为齿向载荷分布系数(齿轮运行中的齿向误差),经过计算KFβ=1.15。
Yx为尺寸系数,根据《齿轮手册》弯曲强度尺寸系数表选择 Yx=0.666。
J2为齿轮弯曲强度几何系数(根据《齿轮设计手册》中“弧齿准双曲面齿轮弯曲强度几何系数”J1和J2插值表并依据齿轮参数偏置距 (mm) :E;被齿凸凹面压力角之和 (Deg) :α;齿轮精度等级:IQ ;被动齿轮平均压力αp;被齿大端分度圆直径Ø等参数确定为0.259。
Z1为主齿齿数;
Z2 为被齿齿数
b2为被齿齿面宽
d2为被齿大端分度圆直径
mt2为被齿大端端面模数
T为发动机功率(N.m)
将以上参数代入以上公式计算得到齿轮齿根应力ϬF=216.64MPa,小于该材料的极限应力207MPa(由《齿轮传动手册》中“试验齿轮齿根弯曲疲劳极限应力”查得)。
结论:
1、当发动机功率T1为190N.m时, ϬF=178.96Mpa,ϬF<ϬFim=207Mpa
2、当发动机功率T1为230N.m时,ϬF=216.64Mpa>ϬFim=207Mpa,安全系数SFmin=0.955,即齿轮工作时所受的应力大于材料的极限应力,从而造成被动齿轮断齿。
分析结果:
通过对故障件原材料、齿形缺陷及热处理方面分析,均未发现异常,且产品加工过程受控;通过对该产品的强度计算得出:当汽车发动机功率增大到230N.m时,该被动齿轮的齿根应力设计弯曲强度安全系数为0.955<1.0(通过查询《齿轮设计手册》可以知道,对于齿轮设计时最低的可靠度要求齿根弯曲强度安全系数SFmin≥1)。所以决定对齿轮设计进行改进,提高齿轮副的安全系数,从而提升产品的可靠性。
三、设计优化
1、设计优化思路
根据驱动桥齿轮设计的相关要求,驱动桥后桥齿轮承受的强度须小于该材料的许用强度,且安全系数>1.0,由被动齿轮安全系数的计算公式
SF =ϬFimYNT/(ϬFYθ)
YNT为被动齿轮的寿命系数,该系数是由齿轮的设计寿命决定的,与齿轮本身的制造无关。
Yθ为齿轮工作时的温度系数, 该参数是由齿轮在运转过程中差检壳中油池的油温所决定的。
Ϭfim为材料的弯曲极限应力,该参数是由材料和热处理条件决定的,是经过实验得来的(见齿轮弯曲极限应力表)。
ϬF为齿轮的计算齿根弯曲极限应力,根据齿轮和发动机的功率等参数计算得出的
即SF =ϬFimYNT/(ϬFYθ)=207/ϬF>1
所以,后桥被动齿轮所承受的齿根弯曲应力ϬF应小于207N.m,才能保证SF>1。
由齿轮强度齿根应力计算公式可以得出要减小齿根应力ϬF,需要改变齿轮的几何参数,因为发动机输出功率和齿轮安装及使用条件所限,而齿轮的参数也受到差减壳空间及安装位置所限,所以对于被动齿轮来说,只有齿形系数J2可以改变,而J2 是通过《齿轮弯曲强度几何系数线图》 查询。该线图的绘制是根据齿轮的压力角ɑ和偏置距及分度圆直径的比例(E/d2)绘制的,所以J与压力角ɑ 、偏置距E和分度圆直径d2有关。而E、 d2受差壳与检壳的位置所限制,不能改变,只有齿轮的压力角这个变量可以改变。
通过观察《齿轮弯曲强度几何系数线图》(如下图)发现,对于同样的主动齿数(10),被动齿轮几何系数 J2随齿轮压力角的增大而增大。由此可知,增大齿轮压力角可以减小齿轮的计算齿根应力ϬF ,进而增大齿轮的弯曲强度。
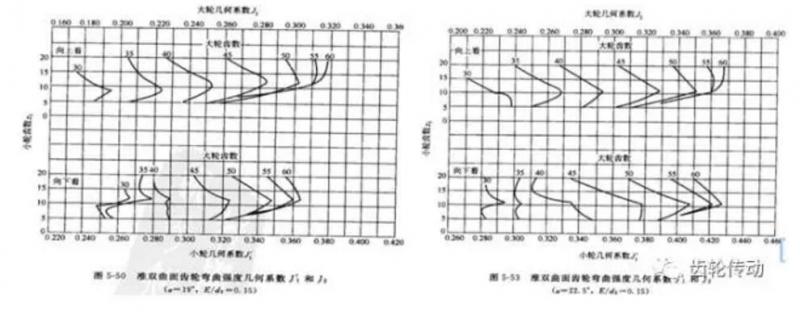
2、压力角设计条件
由于齿轮压力角属标准压力角,而压力角的改变将直接影响着齿轮的制造加工质量,根据《齿轮设计手册》可以知道压力角能齿轮加工质量的影响(如下表)。
汽车齿轮压力角设计
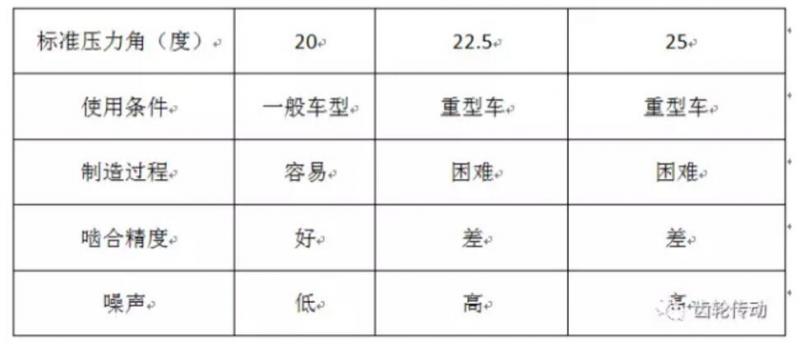
分析:
对于该越野车型,压力角可以在20-22.5度之间选择,但是压力角越大,制造越困难,齿轮的啮合精度越差,噪声越高。经过综合考虑,决定采用21˚15′的压力角,同时该压力角又是标准6"切齿刀的压力角。选择6"切齿刀可以实现减小齿轮的计算齿根弯曲强度,增大齿轮齿根弯曲强度的安全系数。
3、改进—齿轮齿形
经过对压力角的设计条件分析可以得出,对该越野车形齿轮压力角进行改进,平均压力角由改进前的 19˚变为改进后的21˚15΄对于弧齿锥齿轮来说,改变齿形是通过改变切齿刀具来实现的,由于刀具的改变,该齿轮的工作齿高及中点螺旋角也有相应的变化,但不会产生其他影响。
切齿刀具改变后,该齿轮的轮齿的工作齿 高由改进前的 9.09 变为改进后的8.35;中点螺旋角由改进前的 30˚ 02 变为改进后的 32˚ 36΄。
4、改进后的齿轮强度计算
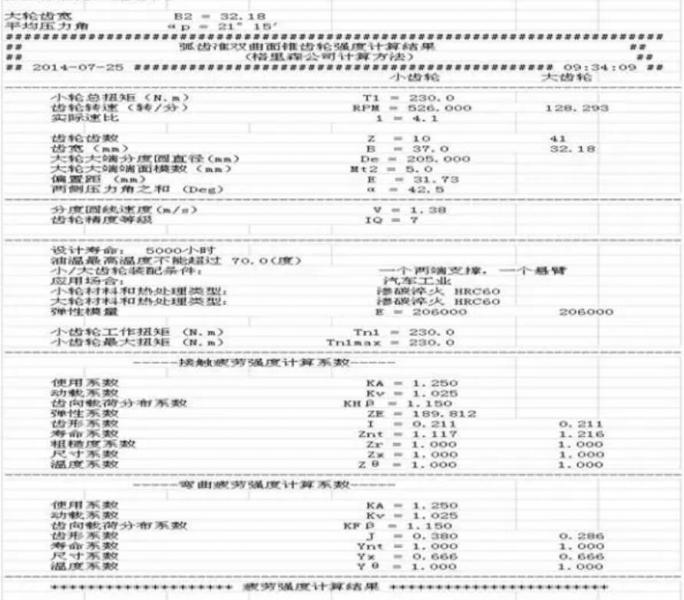
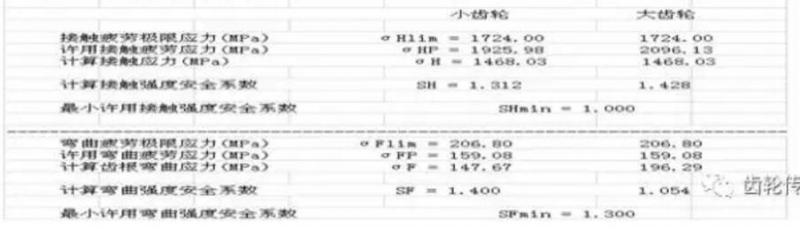
改进结果:
通过对该产品的刀具进行优化改进(切齿刀具由7.5"更改为6"),当发动机功率由190N•M增大到 230N•M时,该产品主动齿轮安全系数由改进前的1.264增大到了1.4;被齿安全系数由改进前的0.955增大到了1.054,在一定程度上,提升了齿轮的齿根应力,降低了断齿风险。
四、对改进后的齿轮装配啮合质量进行验证
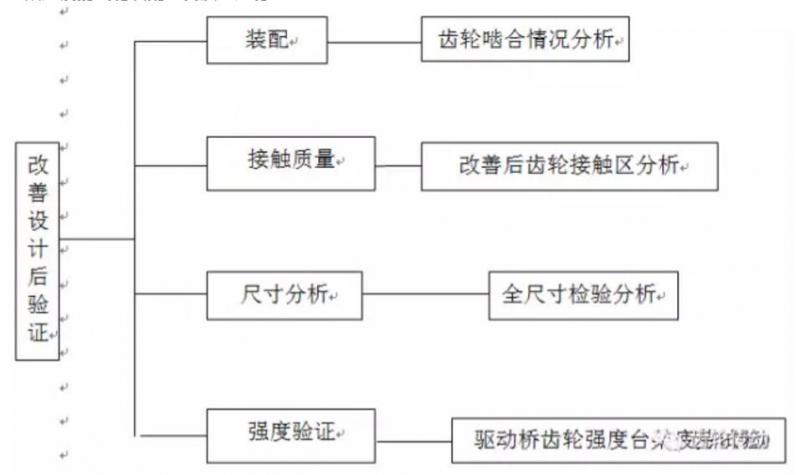
1、齿轮啮合质量
将齿轮模拟行驶情况装在齿轮滚动检查机上检测齿轮啮合干涉验证,通过在齿轮滚动检查机上模拟实际装配情况对齿轮的啮合接触质量进行验证,产品转动灵活且无干涉,运转平稳。
2、对改进后的齿轮接触区进行分析
通过检测,齿轮接触区的位置如下:
接触区域在齿中部偏小端长度约占齿长的50%,宽度约占整个齿高的80%.齿顶、齿根均能脱开0.5mm左右,且未参与啮合,因此该部位不会发生磨损、变形等,满足齿轮技术要求。
3、齿轮的几何尺寸
通过对改进后的主被动齿轮进行全尺寸检验,改进后的主被动齿轮几何尺寸全部能控制在技术要求范围之内, 检测结果均合格。
4、对改进后的齿轮副作台架疲劳试验进行验证
依据QC/T 533—1999汽车台架试验方法,按发动机最大扭矩计算与按最大附着力计算,取两者中较小的一个。
1、按发动机最大扭矩计算,通过分动器以传动系最低档传动时作用于后桥齿轮上转矩(Nm) 为:Tse=Tmax*iTL/*Ko*ŋT/n=3781.02 N•M
2、按最大附着力计算,驱动车轮打滑时作用于主动齿轮上的转矩(Nm)为:Tss=G1*Ø*rr/iLB/ŋLB=4378.48 N •M
目标:依据QC/T 534-1999汽车驱动桥台架试验评价指标要求,台架疲劳寿命≥5ⅹ10⁵。
检测报告如下:
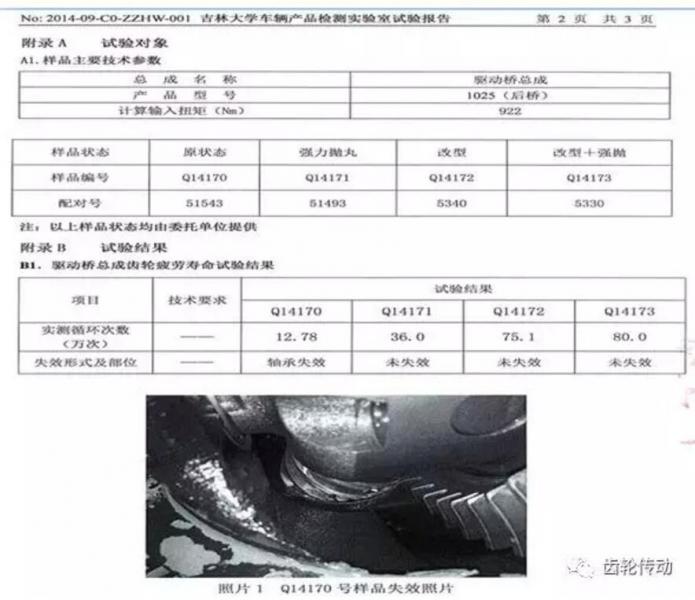
结果:
经过试验发现,改进后的齿轮疲劳寿命远远超过了标准的技术要求。
五、依据IATF16949标准要求对改进后的齿轮进行风险分析
1、失效风险评估
改进前:根据打齿时间为2013年,全年共装齿轮15248套,失效5套。经过台架疲劳试验寿命为12.78万次,按13万次计算,失效概率为PPM=327.9;
改进后:台架疲劳试验寿命为75.1万次,按75万次计,失效概率为PPM=56.8。
2、安全系数规定
如果供需双方没有规定,将按国家标准QC/T 534-1999汽车驱动桥台架试验评价指标执行,如果对可靠度有要求的,一般弯曲强度安全系数要达到1.3以上,由本项目分析可知,需要减小齿根应力ϬF
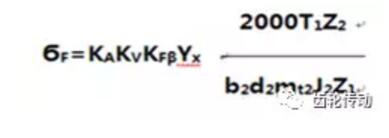
由以上计算公式看出,如果增大齿轮的设计参数b2、d2、mt2、J2、Z1或者减小T1、Z2,可以减小ϬF,增大安全系数SF。
方法①:增大b2、d2、mt2,车桥的桥壳就需要加大,如果改变Z1和Z2,则汽车的设计时速就与显示的不一致。如果汽车的时速及底盘设计不改变,T1、b2、d2、mt2、Z1、Z2是不能改变的。
方法②:增大压力角
所以只有通过增大J2来保证SF,也就是说要增大ɑ和E/d,要增大E/d同样也会改变差检壳的位和大小。只有通过增大ɑ来减小ϬF,增大SF。对于风骏皮卡车型的齿轮压力角ɑ只能选择20-22.5度之间,但是随着压力角的增大,齿轮啮合的重合度降低,重叠系数减小,齿轮的加工困难是增大的;齿轮接触精度也随着压力角的增大而降低的;齿轮装在车桥之后,运转的噪声也由于重合度低而变高,还有可能出现异响。
考虑到加工及齿轮的接触质量、运转平稳性等指标,本项目中决定选择压力角为21˚15′,已再无提升空间。
要继续提升产品可靠性质量,将PPM降低到0,就需要从桥壳、齿轮等产品进行系统改进。
结束语:
对于齿轮失效的质量问题,要从根本原因上去查找。首先对问题进行“项目界定”,之后再对界定的项目进行“项目测量”,查找出问题之后再从失效机理开始分析对产品的功能分析之后进行“设计优化”,整个分析完成之后要对设计优化后的产品进行“设计验证”,如果可行,还要对改进后的产品进行“风险分析”。
为了使改进后的产品质量稳定,还要对问题分析改进的措施形成文件,并将这些问题写进DFMEA或PFMEA中进行控制,以得到持续改进的目的,在日常生产工作中,只有《质量工具》得到了良好的应用,及时修改CP、DFMEA、PFMEA等动态文件,生产的产品质量才能稳定。(高永强 齿轮传动)