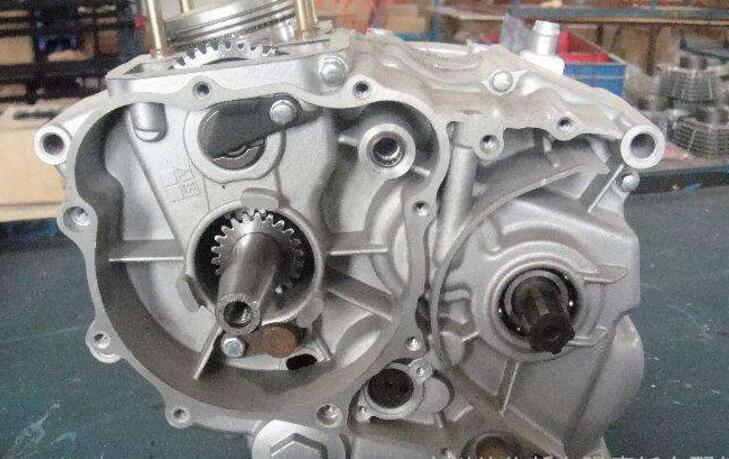
概述
铝合金压铸件在制造业的运用已趋于成熟,并得到广泛的运用,以摩托车为例,诸如:轮毂、汽缸头、缸体、曲轴箱、活塞、曲轴箱盖等均已完成铝合金化。摩托车曲轴箱铝合金压铸是通过高速、高压将铝合金溶液高速压入参照产品图纸设计开制的模具型腔内,并施以保压凝固成型,再脱模取出。在该过程中基于铸造工程参数的控制实现整个过程的稳定性及过程控制。
铝合金压铸件具有质量轻、性能好、生产效率高、表面质量好、尺寸精度高等诸多优点。但在实际生产中出现的品质问题也十分突出,如花纹、流痕、冷隔、充型不良、夹渣、压检不良、气泡、多肉、裂纹、欠铸、烧蚀、粘模、气缩孔、飞皮等,缺陷形成有多方面的原因,必须找到问题出现的原因才能作出正确的判断,才能提出有效、可行的改善对策。
本文主要以摩托车曲轴箱压铸件加工过程中出现的压检不良现象为研究对象,针对其压铸过程中可能造成的原因进行分析寻求解决对策。
1、 压检不良
压检是在箱体加工完成后对油道部分进行气密性检查的工序过程。压检原理:是指在气密性检查时,空气填充过油区域,通过对比输入压力与反馈压力的差值进行气密性判断。区域存在空气泄漏时,致使反馈的压力与输入压力存在差值,当差值超过规定范围值时报警灯亮起,反映出工件压检不良,需对工件进行水检查找漏点,能发现漏点的工件需区分并报废处理。
针对我公司生产的125型曲轴箱1压检工程如图1所示,压检区域如图2所示部分,压检不良确认的漏点如图3所示,且该种箱体漏点均是同位置。
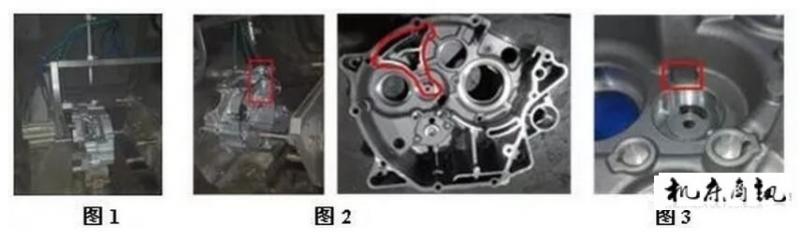
1.1压检不良的影响
压检不良比例约为15%,不仅对品质有影响也对生产工时有影响。
1.1.1压检不良影响品质
压检不良就是反应箱体油道内存在非正常泄漏点,在正常工作时机油对发动机进行润滑,油道就是定向满足机油对各需要润滑部位进行润滑。若存在小漏点因压力损失远小于机油泵输出的压力,不会造成发动机异常,但会引起机油发泡;若存在足够大的泄漏点,会严重损失油压致使机油无法达到缸头、缸体进行润滑,可能造成发动机拉缸,从而停止工作,带来安全隐患。
1.1.2压检不良影响工时
当压检不良指示灯亮起时,压检夹具连同工件会自动沉水检查漏点。每次沉水检漏过程需平均耗时30S,当沉水比例较大时,是无法完成正常生产计划的。
2、压检不良现象原因分类
压检过程主要涉及三部分:工件、夹具、气源控制系统,出现压检不良需要分三方面对其进行检查、确认。
2.1气源控制系统
生产线气源控制系统是一定的,通用于生产所有型号箱体的压检过程,在生产其他箱体时未出现压检异常,且设备维修组对其进行点检确认无异常,从而排除气源控制系统异常直接引起压检不良。
2.2压检夹具
压检不良就夹具而言,当其封堵不严密时会自然泄气造成压检不良,确认现象时对夹具进行密封垫全套更换以排除破损、变形造成不良。另外,针对夹具专门制作了125型曲轴箱1的压检标准样件,用于在生产时对夹具进行有效性确认,可以排除夹具造成压检不良现象。
2.3加工件
排除气源控制系统、夹具等因素,明确压检不良是来至于工件本身。
3、产生原因分析
目视确认漏点位于非加工面上,应为铸造过程出现的缺陷问题。由于水检现象时连续的圆形水泡(若为穿透性裂纹水检现象因为沸水翻滚状),且作色渗透检查无线形作色剂残留,可排除该处不良是穿透性裂纹引起。从铸造工艺调整方面入手,以 4M为基础进行压检不良原因的分析。
3.1铝材成分
铝液成分异常可引起凝固组织疏松,另外含渣、含气量大亦可能形成渣孔、气孔,造成凝固后组织不致密。检测铝材成分如下表1:

实际铝液除渣操作按工艺要求执行,除渣周期为1次/2小时,且造渣剂(除渣、除气混合剂)与铝液比例按0.3%投放进行除渣、除气。该工艺通用于所有箱体制造生产,而其他车型箱体无压检不良,侧面证明非铝材原因造成压检不良现象。
3 .2铸造压力
铸造过程中铸造压力不足时,铸件致密程度受影响,铝液的膨胀性很大,压力不足时有足够的区域与时间形核并长成枝晶状,而在晶界面凝固收缩就会形成疏松,尤其是在非直接压力方向上,通过后续的保压是改变不了组织形态的。在后工序加工后压检时会因组织疏松形成泄漏。
3 .2.1压力改善及效果
正常生产时铸造压力为640±20Kg/cm2,分别调整为600 Kg/cm2、700Kg/cm2、730Kg/cm2进行生产试验,试验数量为各20件,直接进行加工确认压检不良比例,结果为:600 Kg/cm2试样不良6件,占比30%,另外,铸件远端表面存在冷隔、褶皱,影响铸件外观;700Kg/cm2试样不良7件,占比35%;730Kg/cm2试样不良11件,占比55%。验证结果:压力改善对铸件压检不良无改善效果。
3 .3铸造速度
铸造速度分:第一阶段速度、第二阶段速度。第一阶段速度过高,在压射过程会形成卷气进入铝液,并最终分散在铸件内部形成气孔;第一阶段速度过低,会降低铝液温度、降低铝液的流动性,开始形成晶核并长大,在后期的高速压射时已无法均匀形核,较大的晶核会造成铸件断面质点粗大不均匀,夹渣、夹气后内部组织不致密。第二阶段速度过低,导致浇口速度不足,铝液以流状进入充填,冲填时间过慢,形核长大造成组织粗大[2]。实际高速为2.5-2.8m/s,不会出现速度过高情况。
3 .3.1速度改善及效果
低速度为0.15±0.05m/s,处在相对较小值范围,本次验证未对其进行降速试验。将第二阶段速度提高至3.0m/s、3.2 m/s,分别试作20件试样进行压检确认,不良比例分别为25%、15%,对压检不良没有改善效果。
3 .4冲头润滑油
冲头油在压铸过程中对活塞与料筒进行润滑,当冲头油滴在料筒时,注入铝液会起明火燃烧,产生气体。当前正常生产状态中冲头油滴注在冲头上方,在冲头运行中进行润滑,但在连续生产中冲头润滑油仍会积累,在注入铝液时明火燃烧,产生气体进入型腔,增加铸件内部气孔含量。
3 .4.1冲头润滑油改善及效果
为了减少润滑油的积累并更均匀的润滑料筒内壁,采用喷雾方式供给润滑油并将单次油量降低至3ml。试验20件,加工压检不良数为5件,不良占比25%。冲头润滑油供给方式改变及油量下降对压检不良无改善效果。
3.5铝液温度
生产中铝液温度对铸造影响十分重大,当铝液温度过低时,铸件成型不够充分,在结构复杂及薄壁处体现尤为明显;当铝液温度过高时,凝固时间延长,同时模具温度升高,致使在肉厚及热结部位最后凝固。从曲轴箱压检不良漏点来看,该处正处于热结区域。
3 .5.1铝液温度降低及效果
原始铸造铝液温度为675±15℃,当温度处在下限时,压检不良仍然出现。验证时设置铝液温度为640℃,试作试样20件,不良数量为3件,占比15%。结论:以降低铝液温度来改善该处压检不良效果不明显。
3.6 模具温度
模具温度涉及三方面(模具冷却水、离型剂吹附、铝液温度)的影响。在上述3.5中已排除了铝液温度的影响。如模具冷却水出现堵塞,会导致局部温度异常升高,仅靠离型剂降温是远远不够的,此时铸件该位置处为最后凝固区域,可能出现气缩孔。如离型剂吹附不均匀或量不足时,会出现铸件拉模及烧附粘铝,破坏铸件表面硬质层,当另一硬质层面被加工时,极易出现压检漏气。
3 .6.1模具温度改善及效果
(1)检查确认模具冷却水均无堵塞,且与其他机种模具流量近似;(2)对应铸件压检不良的型腔区域,增加离型剂铜管吹附数量(1-2支),模温测量如图5所示,试作样件30件(离型剂量大模温上升缓慢),出现压检不良4件;延长1-1.5s吹附时间,试作样件表面冷隔严重,未作压检工序验证。
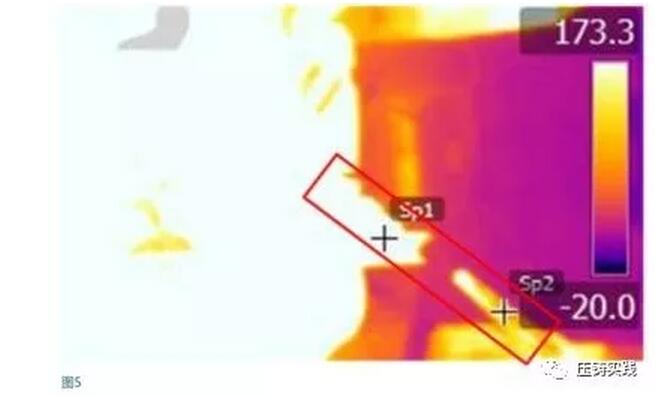
3.7 铸造工艺调整总结
对铸造过程中多个能造成铸件压检不良的重要因素进行原因分析及改善试验,均无明显改善效果。从铸造理论而言,上述影响因素的调整应取得一定效果,实际情况则表明在大的范围里,上述因素的调整带来的效果可能微乎其微。在工艺验证的基础上,进而展开对产品结构及制造模具的检讨,以寻找到有效改善的对策。
4、加工余量
由于铸造品尺寸精度较低而且存在收缩性,一般收缩率为5/1000,为了满足装配性等尺寸精度要求,在设计模具时在产品具有装配、精度要求高的局部增加加工余量,再通过加工去掉余量,得到符合要求的尺寸精度。
4.1 加工余量确认
对比加工完成品及毛坯实物,油道路径LD68孔(如图6)是需要加工来保证尺寸。在漏点部位(如图7)解剖两种状态部品作截面尺寸对比如下图8、图9,确认远端孔加工单边余量为2.5mm左右。这与压铸中毛坯加工余量《1mm相悖。确认图纸设计孔的加工余量为单边0.75mm,由于该孔长度为102mm、拔模斜度为1.5°,导致上述LD68孔加工余量过大情况。压铸件存在气孔,加工余量过大会使内部气缩孔暴露,LD68孔油道压检不良与之可能存在相关联系。

4.2 加工余量改善及效果
改善方案:减小LD68孔加工余量。根据毛坯图纸LD68孔尺寸,孔深度是有装配关系要求的,在考虑拔模能力时,将型芯拔模斜度减小至1°,可将远端单边加工余量减小0.85mm,尽可能避免内部气孔暴露。
将拔模斜度为1.5°的型芯更换为拔模斜度为1°型芯,生产工艺条件正常设置,试生产40件,无压检不良出现。为了确认改善效果的稳定性,进行了批量验证,生产中无异常情况出现,该处漏点亦无压检不良出现。
5、 结束语
压铸件加工后出现压检不良问题是较为常见的现象,有时候调整工艺参数是能解决的,但并不是都靠工艺参数能解决。具体问题需要具体分析,找到本质的原因才能直接、有效的对策。该125型曲轴箱1压检不良,经验证得出是因为较大的加工余量致使热结部分气缩孔暴露,与非加工面出现粘模现象同时发生,产生的漏气现象。经过改善减小加工余量,提高加工面的致密度,可消除压检不良。当然,不同产品、不同结构处的压检不良应具体分析,寻找切合实际的解决方案。
本文作者:重庆建设·雅马哈摩托车有限公司 铸造技术部 罗久林、唐和雍